Surface finishing
Flexmill’s robot system can utilize the grinding and polishing tools for the surface finishing and the milling tool for finishing edge contours and areas used for connecting a part from a potential previous process step to the milling machine.
With force control, the tools will accurately follow the surface for the best results.
The system consist of one large payload force controlled robot system and a high precision rotary servo table.
The finishing process is completed by utilizing the Electrical Spindle Motor mounted on the active force compliance unit and a variety of different grinding disks and stones.
Flexmill’s patented fully automatic disk change system improves the autonomy of the system and an unmanned production time of up to up to 24 hours can be achieved
Controlled propeller finishing process
- Measuring
- Best-fit operation with CAD model
- Programming with CAD/CAM
- Controlled grinding- Adaptive material removal based on measured information
- Milling of edge contour
- Finishing
Pattern machining for molds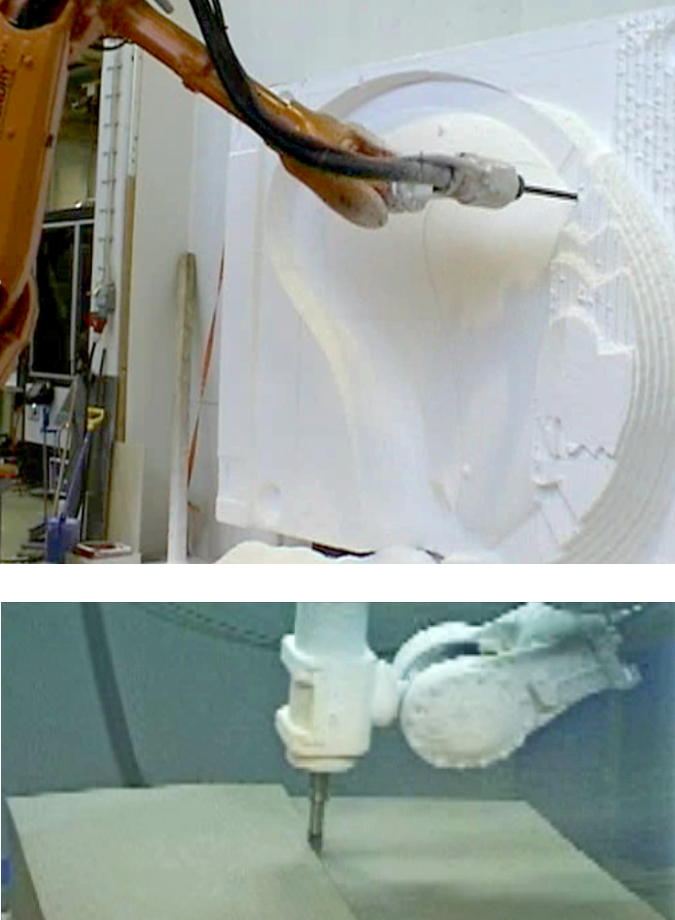
The Flexmill robotized platform is well-suited for machining all kinds of pattern materials such as expanded polystyrene, high-density structural foams, tooling paste, wood etc.
The typical process equipment used for pattern machining in the Flexmill robot system include:
Hollow shaft spindle motor
Debris vacuum system
Direct mold milling
Instead of using patterns, molds can be machined directly to the sand. This will increase the flexibility in production.
The following equipment is typically utilized in the Flexmill robot system for direct mold milling:
Spindle motor
Waste sand handling system
Dust vacuum system if necessary